Read time: 3.5 minutes
The task is simple, or so it seems. You’re under the weather and need to visit your local community pharmacy or nearest retail chain to grab an over-the-counter medication for some much-needed relief. Maybe it’s an antibiotic or specialty prescription used to treat your chronic condition. No matter the situation, behind the task of picking up that medication is an integrated distribution network led largely by McKesson. In fact, one-third of the total pharmaceutical volume in the U.S. are picked, packed and shipped from McKesson’s 25 pharmaceutical distribution centers (DCs) located across the country.
In this fast-paced world of pharmaceutical distribution, efficiency, accuracy and employee well-being are paramount. That’s why over the past year, McKesson has opened two new DCs integrated with innovative technology and designed with sustainable upgrades in both facilities.
“Our latest DCs redefine distribution excellence and seamlessly blend advanced innovations with a commitment to our customers, our employees, and our environment,” says Todd Kleinow, vice president of strategic distribution experience, McKesson.
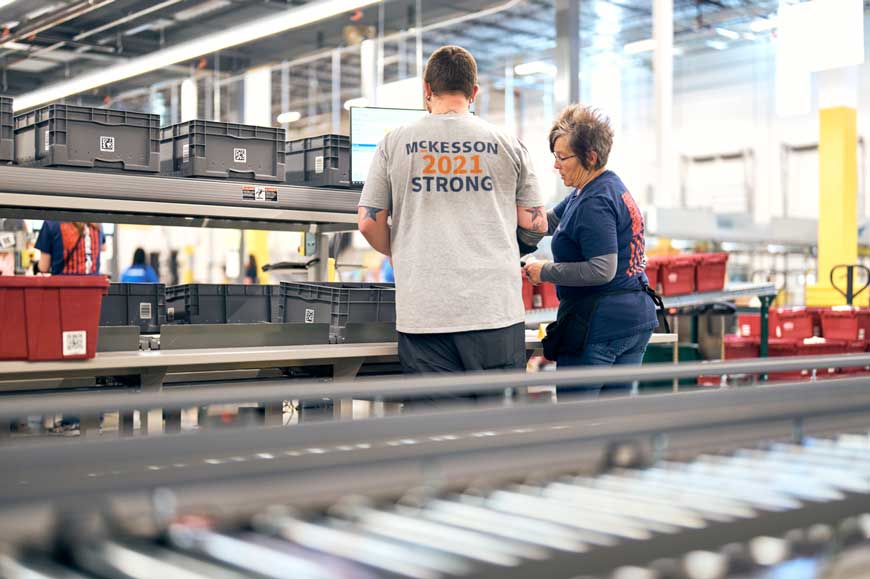
McKesson frontline employees complete the receiving and put away of goods.
Optimizing Efficiency and Customer Service
Through deep experience and innovative thinking, McKesson has continued to meet the growing needs of customers. With this longstanding goal in mind, McKesson has equipped its newest DCs with advanced automation technology that revolutionizes the distribution process.
Inside McKesson’s “ultra” DC located in Central Ohio, an average of 17,000 reusable plastic totes, which are integral to the pick, pack, and ship process, are shipped to customers every day. The totes travel across more than three miles of energy-efficient conveyer belts – starting from the packing locations and ending at the shipping stations. Smart technology scans each tote throughout multiple checkpoints and resolves discrepancies to keep orders moving. An automated pick process, tote washer and storage systems were built to seamlessly handle volume increases and growth over time.
McKesson also opened its Clermont DC in Kentucky to process McKesson Plasma and Biologics orders, such as plasma-derived products and other specialty drugs at competitive prices. Similar to the Central Ohio DC, the Clermont DC was purposefully designed from end to end with customers in mind and is fitted with highly automated processes to improve efficiency and capacity, all while enhancing the overall customer experience.
“Ultimately, our goal was to integrate technology that makes the process of receiving products and life-saving medications easier, faster, and more efficient for our customers and their patients,” Kleinow explains.

An advanced robotic arm palletizes customer orders to prepare them for outbound shipping.
A Space Designed for Our People
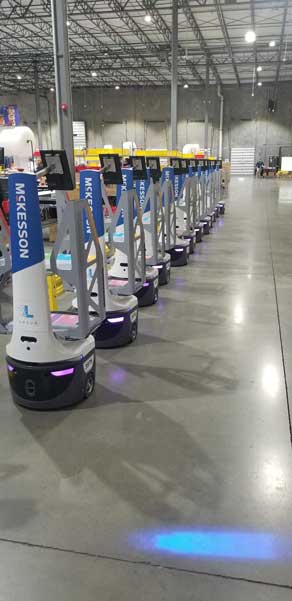
Locus Robots lined up inside a McKesson DCs.
Recognizing that McKesson’s employees are the backbone of its success, the company has prioritized their well-being within these new DCs.
The same automated technology that enables the DCs to pick, pack and ship medications to customers faster also helps reduce redundant and labor-intensive work, optimizes employees’ productivity, and allows them to focus on more meaningful work that advances their skills. For example, the new DCs are equipped with advanced robotics. In the Central Ohio DC, robotic arms automatically shrink wrap and secure pallets before they are loaded and shipped to customers and, ultimately, to patients. And in the specialty Clermont DC, autonomous mobile robots help pick orders and carry them to shipping locations within the DC – reducing the amount of manual transport throughout the facility and ultimately increasing the number of orders employees can fulfill.
“Our employees are the driving force behind our success, which is why we prioritized designing an environment that provides the best possible experience,” Kleinow says. “Those on the frontline can now focus on more fulfilling responsibilities that directly impact customer orders. We’ve also installed a number of amenities designed to create a healthy, comfortable, safe and positive work environment.”
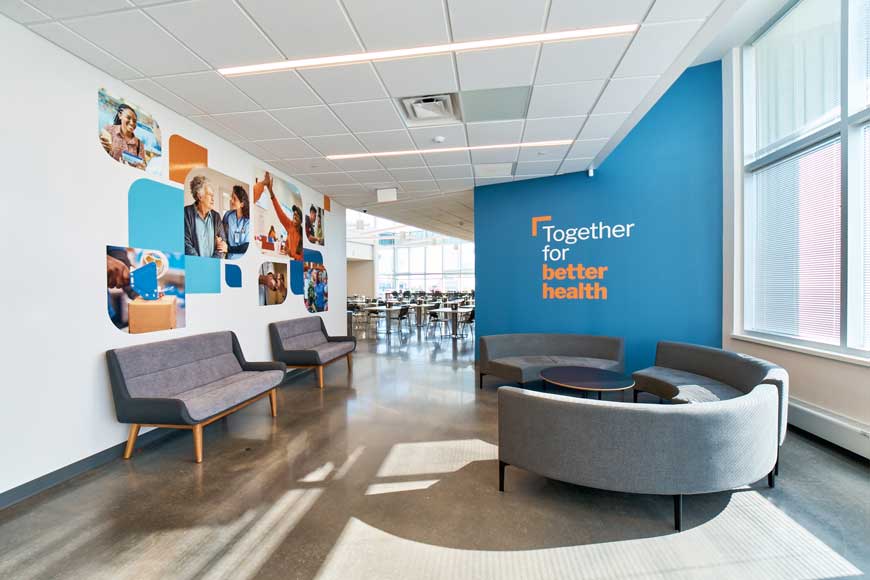
Windows line common areas, allowing natural light to fill the space.
High-bay windows – a rarity in warehouses – allow ample natural light to flood the workspace, which has been shown to boost employee mood and productivity. Additionally, the Central Ohio DC features a walking trail on the property, allowing employees to take breaks outside, promoting both physical and mental well-being.
The new DCs have increased capacity in their training rooms as well, providing employees with opportunities for continued professional development and growth.
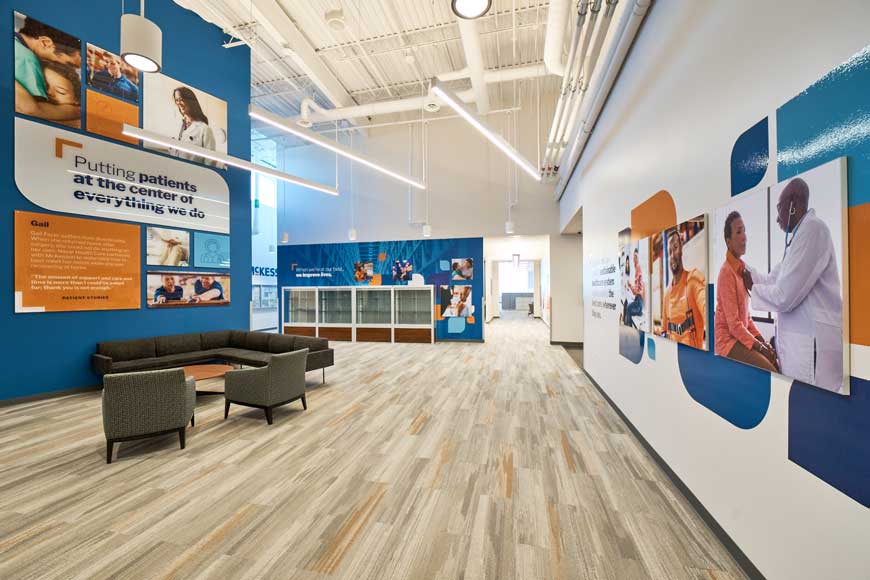
Training rooms and meeting spaces are designed to help employees advance their skills.
Looking to the Future of Distribution
With its newest DCs, McKesson remains at the forefront of supply chain innovation. As McKesson looks ahead, it continues to embrace new technologies like artificial intelligence and machine-to-machine communication to improve operational excellence.
“If you look forward 15 years or so, these are the type of facilities that will carry McKesson into the future,” Kleinow says. “We really found the right recipe with these DCs to make that difference and to advance health outcomes for all.”
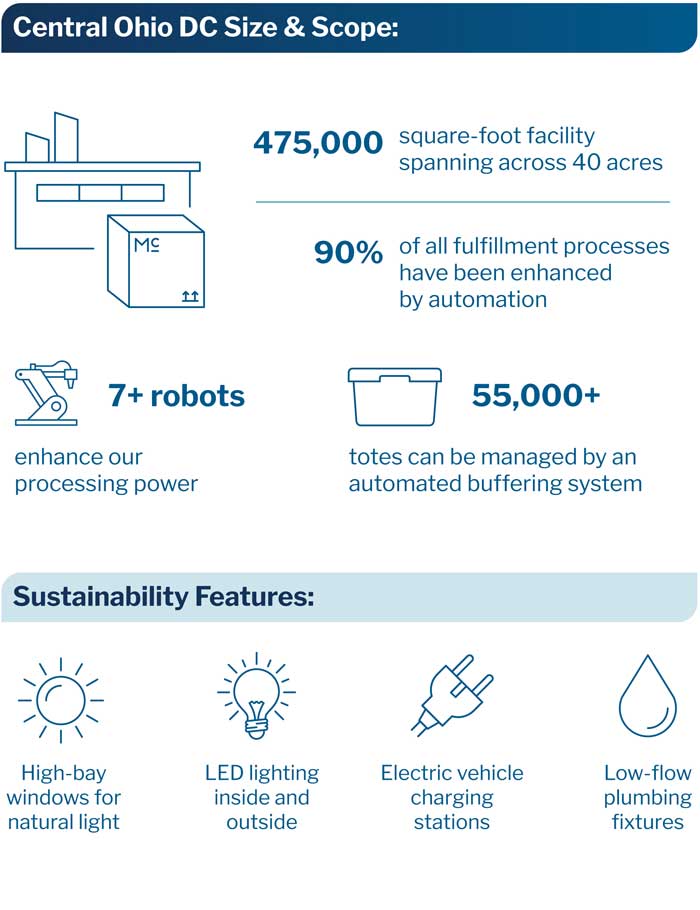
Share
Post
Post
Email